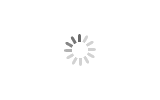
- Kyushan
- China
- 3-5 working days
The bucket is a structural product, consisting of tooth base plate, bottom plate, side plate, wall plate, hanging lug plate, back plate, bucket ear plate, bucket ear sleeve, bucket tooth, tooth seat, guard plate or bucket angle and other excavator bucket parts.
Therefore, welding is the key manufacturing process of the bucket, and the welding quality directly affects the structural strength and service life of the bucket. Today, Kyushan explained the classification and function of excavator bucket parts.
All Kinds Of High Quality Excavator Bucket Parts For Sale
Name | High Quality Customized Excavator Bucket For PC200 Komatsu |
Product Number | All Part Numbers You Need |
Condition | Original Brand New |
MOQ | 1 Piece |
Payment | T/T, Western Union, Paypal, etc |
Standard or Nonstandard | Standard |
Delivery Time | In 3 Days |
Packing | Wooden Box |
Warranty | 6 Months |
Transport | By sea/air/express (DHL/FEDEX/TNT/UPS/EMS/City-line) |
Welding process of bucket body and bucket teeth of excavator
1. Preparation before welding
First, cut off the worn bucket teeth from the bucket body, and then use an angle grinder to clean the installed bucket teeth without dirt and rust, and carefully check whether there are cracks and other defects; use a carbon arc on the bucket teeth to be welded Gouge out the bevel and clean it with an angle grinder.
2. Welding
①First, use GBE309-15 electrode for surfacing on the bucket body (joint with bucket teeth). Before welding, the electrode should be dried at 350℃ for 15h. The welding current should be larger and the welding speed should be slower to ensure the fusion zone. The nickel content is 5% to 6% to prevent the formation of martensite sensitive to cracks.
② Perform tack welding. After the bucket teeth are assembled in place, use the D266 electrode with a diameter of 32MM to carry out symmetrical tack welding on both sides, and the length of the welding seam does not exceed 30MM. Water cooled and hammered immediately after welding.
③ Bottom welding. Use a D266 electrode with a diameter of 32MM for bottom welding. Use small current, DC reverse polarity, intermittent welding, and short-segment welding. Water cooling should be carried out in time every time the welding is stopped, and the temperature of the interlayer should be controlled below 50 ℃.
④ Filler welding is performed. After the bottom welding is completed, use D266 electrode with a diameter of 4MM for intermittent welding, the welding current is 160A, and one electrode is welded in 3 to 4 times. Below, hammering is performed to eliminate stress and prevent carbide precipitation; after each two layers are welded, the left and right welds are alternately welded to ensure the symmetry of the welding, until the welding foot reaches 16MM. Check the cracks with a magnifying glass after each welding. If there are cracks, use carbon arc gouging to eliminate them before welding.
We are a comprehensive supplier of excavator accessories, if you have excavator accessories needs, please contact us, we will be glad to receive your inquiry!
Sales Manager:Liam Cheng Wechat/Whatsapp:+8616653175111